In which Fields are MM-Tech butt welders used?
With nearly 25 years of deep cultivation in the field of plastic pipe butt welding machines, MM-Tech has established an excellent reputation in the industry, which thanks to its professional R&D team, mature manufacturing processes, and a well-developed sales system. Our products are exported to many countries and regions including Europe, America, the Middle East, Russia, and Latin America, and play a crucial role in pipeline installation operations in numerous industries such as oil and gas, water supply, as well as chemical engineering.
Taking into account the working characteristics and actual needs of different industries, MM-Tech recommends various butt welding machine solutions. In the application of water supply and sewage pipeline laying, hydraulic butt welding machines can fully meet the operation requirements with their stable performance. When dealing with pipeline installation projects where the pipe diameter is less than 200mm and the wall thickness is relatively small, the manually operated butt welding machines, which are convenient to operate, is the ideal choice.
The installation of oil and gas pipelines has extremely high requirements for welding precision and safety. Therefore, MM-Tech suggests using fully automatic high pressure butt fusion welding machines to ensure that the welding quality meets strict standards. Relying on our profound technical foundation, MM-Tech provides customers with personalized customization services to fully meet the diverse market demands.
Application of butt fusion welding machine in water supply and water treatment
HDPE material is highly resilient, featuring strong dielectric insulation, high tensile strength, superior rigidity, excellent toughness, minimal permeability, and outstanding corrosion resistance. It can withstand temperatures ranging from -60°C to 70°C.
Welding complies strictly with DVS 2207-1 or ISO 21307 (single low-pressure welding standard).
Butt fusion welding machines play an indispensable role in water supply pipelines and water treatment sectors, ensuring the integrity, durability, and seamless operation of the infrastructure.
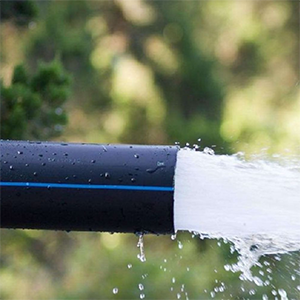
In large – scale municipal water distribution systems, butt fusion welding machines are deployed to connect high – density polyethylene (HDPE) pipes, which are widely favored for their corrosion – resistance, flexibility, and long – term performance. These machines precisely join pipes with diameters typically ranging from 20mm to over 1000mm. For instance, during the construction of new residential areas, they create strong, leak – proof joints, reducing water loss. By preventing leaks, the machines help maintain water pressure, guaranteeing consistent water flow to households and commercial buildings.
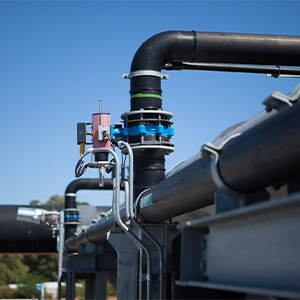
Water treatment plants require a complex network of pipes to transport raw water, treated water, and chemicals. Butt fusion welding machines are used to install pipes that carry raw water from sources like rivers or reservoirs to treatment units. They also create connections for pipes distributing treated water to storage tanks or for final distribution. Additionally, they are essential for welding pipes that handle chemicals used in the treatment process, such as chlorine or coagulants. Since these chemicals can be corrosive, the high – quality welds provided by butt fusion machines prevent leaks, safeguarding the environment and plant workers.
Over time, pipes in water treatment plants may deteriorate due to chemical exposure, mechanical stress, or aging. Butt fusion welding machines enable quick and efficient repairs. When a section of pipe is damaged, workers can cut out the faulty part and use the machine to weld in a new replacement. This minimizes downtime, ensuring the continuous operation of the treatment plant and the uninterrupted supply of clean water.
Application of butt fusion welding machine in drainage and sewage treatment
HDPE material offers superior properties, including strong dielectric insulation, high tensile strength, excellent rigidity, exceptional toughness, minimal permeability, and outstanding corrosion resistance. It can withstand temperatures ranging from -60°C to 70°C.
Welding follows DVS 2207-1 and ISO 21307 (single low-pressure welding standard).
Butt fusion welding machines are essential in drainage and sewage systems, ensuring reliable and leak – free infrastructure. Their applications span from municipal networks to industrial waste management, contributing significantly to public health, environmental protection, and smooth urban operations.
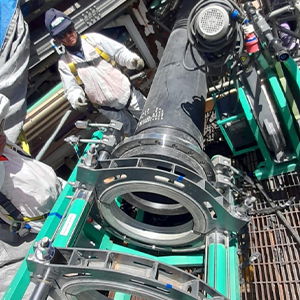
During the construction of new residential or commercial areas, butt fusion welding machines are used to join large – diameter pipes. These pipes, often made of high – density polyethylene (HDPE), form the backbone of the drainage and sewage collection systems. The high – precision welding provided by these machines creates strong, seamless joints that can withstand the pressure of large volumes of wastewater and stormwater.
As cities expand and aging infrastructure needs improvement, butt fusion welding machines play a crucial role in network upgrades. They can be used to replace damaged or undersized pipes, seamlessly integrating new sections into the existing system.
At sewage treatment plants, butt fusion welding machines are used to install pipes that carry raw sewage from collection points to treatment units and treated effluent for discharge. The ability to create leak – tight joints is vital here, as any leakage could lead to the release of untreated sewage into the environment, causing pollution and health hazards.
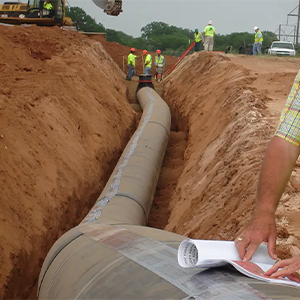
Industrial facilities, such as chemical, food, and automotive manufacturing plants, generate a significant amount of wastewater. Butt fusion welding machines are used to install pipes that can handle the specific characteristics of the industrial effluent. For example, in a chemical plant, where wastewater may contain corrosive substances, pipes made of corrosion – resistant materials like high density polyethylene (HDPE) are welded using butt fusion techniques. The resulting strong and chemically resistant joints prevent leaks and ensure the safe disposal of industrial waste.
Many industries are increasingly adopting wastewater recycling systems to reduce water consumption and environmental impact. Butt fusion welding machines are used to construct the pipelines in these systems, which require high – quality welds to maintain the integrity of the recycled water.
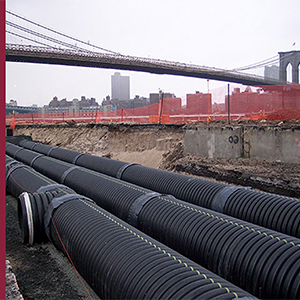
In urban areas, storm sewers are essential for preventing flooding during heavy rainfall. Butt fusion welding machines are used to install large – diameter pipes that can quickly carry stormwater away. These machines can weld pipes with different shapes and sizes, allowing for the construction of complex storm sewer networks. Well – welded storm sewer pipes can handle the large volume of rainwater, protecting buildings and infrastructure from water damage.
Pipes connected to retaining ponds and detention basins, which store and gradually release stormwater, are also welded using butt fusion machines. The proper welding of these pipes ensures that the water flow is controlled and that the basins function effectively in managing stormwater runoff.
Application of butt fusion welding machine in oil and gas
HDPE material is highly durable, featuring strong dielectric insulation, high tensile strength, superior rigidity, excellent toughness, minimal permeability, and exceptional corrosion resistance. It can withstand temperatures ranging from -60°C to 70°C.
Welding is performed strictly according to ISO 21307 (single high-pressure) and ASTM F2620 (high-force standard) to ensure superior welding quality.
HDPE pipe has proven to be the most effective solution in oil and gas gathering applications for over 35 years. Butt fusion welding machines are fundamental to the infrastructure of the oil and gas industry, playing an essential role in pipeline construction, maintenance, and repair processes.
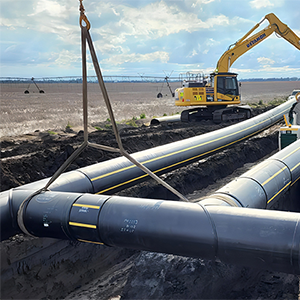
At the epicenter of oil and gas extraction, well – heads are outfitted with a complex network of pipes. Butt fusion welding machines are used to join pipes that carry raw hydrocarbons from the reservoir to the surface. In shale gas operations, for example, high – density polyethylene (HDPE) pipes, renowned for their corrosion resistance, are welded together using these machines. This creates a secure and leak – proof connection, crucial for preventing fugitive emissions, maintaining pressure integrity, and ensuring safe extraction.
Gathering pipelines transport oil and gas from multiple well – heads to a central processing facility. The terrain in oil fields can be rugged and diverse, and butt fusion welding machines enable the installation of pipelines even in challenging environments. These machines can handle pipes of various diameters, typically ranging from 2 inches to 12 inches. The welded joints are robust enough to withstand the pressure fluctuations associated with the collection process.
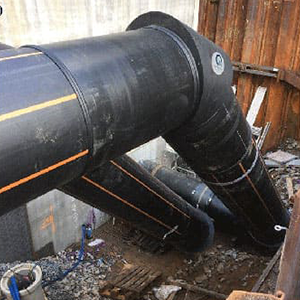
Inside oil and gas processing plants, a complex network of pipes is required to transport raw materials, intermediate products, and finished products. Butt fusion welding machines are used to install pipes that carry highly flammable and potentially hazardous substances. In a natural gas processing plant, for example, where methane is separated from other components, the pipes handling this combustible gas must have leak – free joints. The machines can also create intricate piping layouts, enabling the efficient flow of materials through different processing units.
Over time, pipelines in oil and gas plants may degrade due to chemical corrosion, mechanical wear, or aging. Butt fusion welding machines are vital for both routine maintenance and emergency repairs. When a section of pipe is damaged, the defective part can be removed and replaced with a new segment using butt fusion welding. This helps to minimize production downtime, reduce environmental risks, and ensure the continued safe operation of the plant.
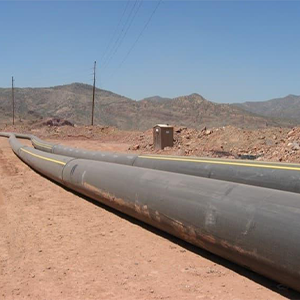
Long – distance onshore pipelines are the arteries that carry oil and gas from production fields to refineries, power plants, and distribution centers. Butt fusion welding machines are crucial for joining large – diameter steel pipes, often ranging from 16 inches to 48 inches. The welding process ensures that the joints can endure high internal pressures, as well as external forces such as ground movement, temperature changes, and mechanical stress. In North America, extensive pipeline networks stretching thousands of miles rely on the high – quality welds created by these machines to maintain uninterrupted hydrocarbon flow.
Application of butt fusion welding machine in mining and industry
HDPE material exhibits exceptional properties, including strong dielectric insulation, high tensile strength, excellent rigidity, outstanding toughness, minimal permeability, and superior corrosion resistance. It can withstand temperatures ranging from -60°C to 70°C.
Welding strictly adheres to ISO 21307 (single high-pressure) and ASTM F2620 (high-force standard).
Industrial-grade piping systems must be able to withstand daily pressure fluctuations and resist the corrosive and abrasive materials that pass through them, such as slurries, acids, and salts common in these applications. HDPE pipe meets these needs with its abrasion resistance, chemical resistance, toughness, leak-free fusion joints, tolerance to variable operating conditions, and excellent long-term performance.
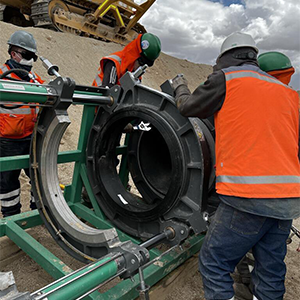
In underground mines, efficient ore transportation is vital. Butt fusion welding machines are used to fabricate and install pipelines for slurry transportation. As ore is often mixed with water to form a slurry for easier movement, the pipelines need to withstand abrasion and corrosion. HDPE pipes welded with butt fusion machines offer excellent resistance to both.
At surface mines like coal mines, long – distance conveyor systems rely on welded components. Butt fusion welding machines are used to join large – sized plastic pipes that carry water for dust suppression. These pipes need to be leak – proof to avoid wasting water resources. The high – quality welds created by the machines ensure that the water distribution system functions effectively, maintaining a safe working environment by reducing dust pollution.
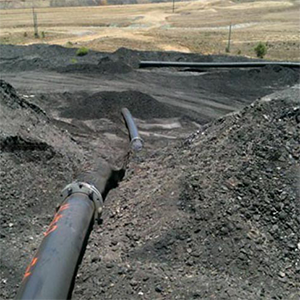
Mines often encounter water inflows that need to be drained to prevent flooding. Butt fusion welding machines are deployed to construct durable drainage pipelines. By creating strong and watertight joints, these machines help in removing groundwater and seepage from the mine. In gold mines, where the presence of water can impede mining operations and cause safety hazards, the reliable drainage systems made possible by butt fusion welding are essential.
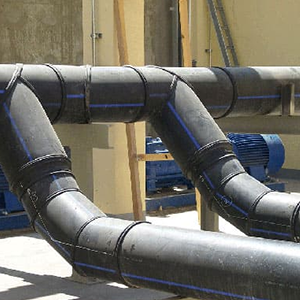
Chemical plants deal with a wide range of corrosive substances. Pipes made of materials like HDPE, PVC, PVDF, and PP, which are resistant to chemical corrosion, are welded using butt fusion machines. For instance, in a fertilizer production plant, pipelines carrying sulfuric acid, a highly corrosive chemical, require welds that can withstand continuous exposure. The precise control over the welding process by butt fusion machines ensures that the joints are chemically resistant, preventing leaks that could lead to environmental pollution and safety risks.
In addition to corrosive fluids, chemical plants also need to transfer process water and steam. Butt fusion welding machines are used to create high – integrity joints in pipes handling these substances. This helps in maintaining the efficiency of various chemical processes by ensuring proper fluid and steam flow.
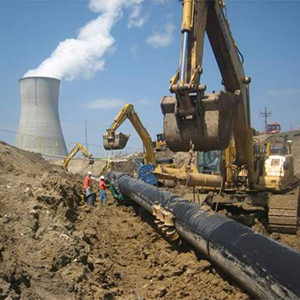
Power plants, whether they are coal – fired, gas – fired, or nuclear, require extensive cooling water systems. Butt fusion welding machines are used to install large – diameter pipes for cooling water intake and discharge. The welded joints need to be robust to withstand the high – volume water flow and pressure.
In coal – fired power plants, ash and slag generated during the combustion process need to be transported for disposal. Butt fusion welding machines are used to construct pipelines for ash and slag slurry transportation, ensuring that these waste materials are safely and efficiently removed from the plant.